Creating a Welding WPS: Step-by-Step Recommendations for Professionals
Creating a Welding WPS: Step-by-Step Recommendations for Professionals
Blog Article
Understanding Welding WPS Criteria: Ideal Practices and Techniques for High Quality Welds
In the realm of welding, mastering Welding Treatment Specification (WPS) criteria is a crucial component that straight influences the high quality and honesty of welds. As we navigate through the details of welding WPS standards, discovering crucial insights and techniques for attaining top-tier welds will be vital for welders seeking to excel in their craft and produce welds that stand the test of time.
Comprehending Welding WPS Requirements
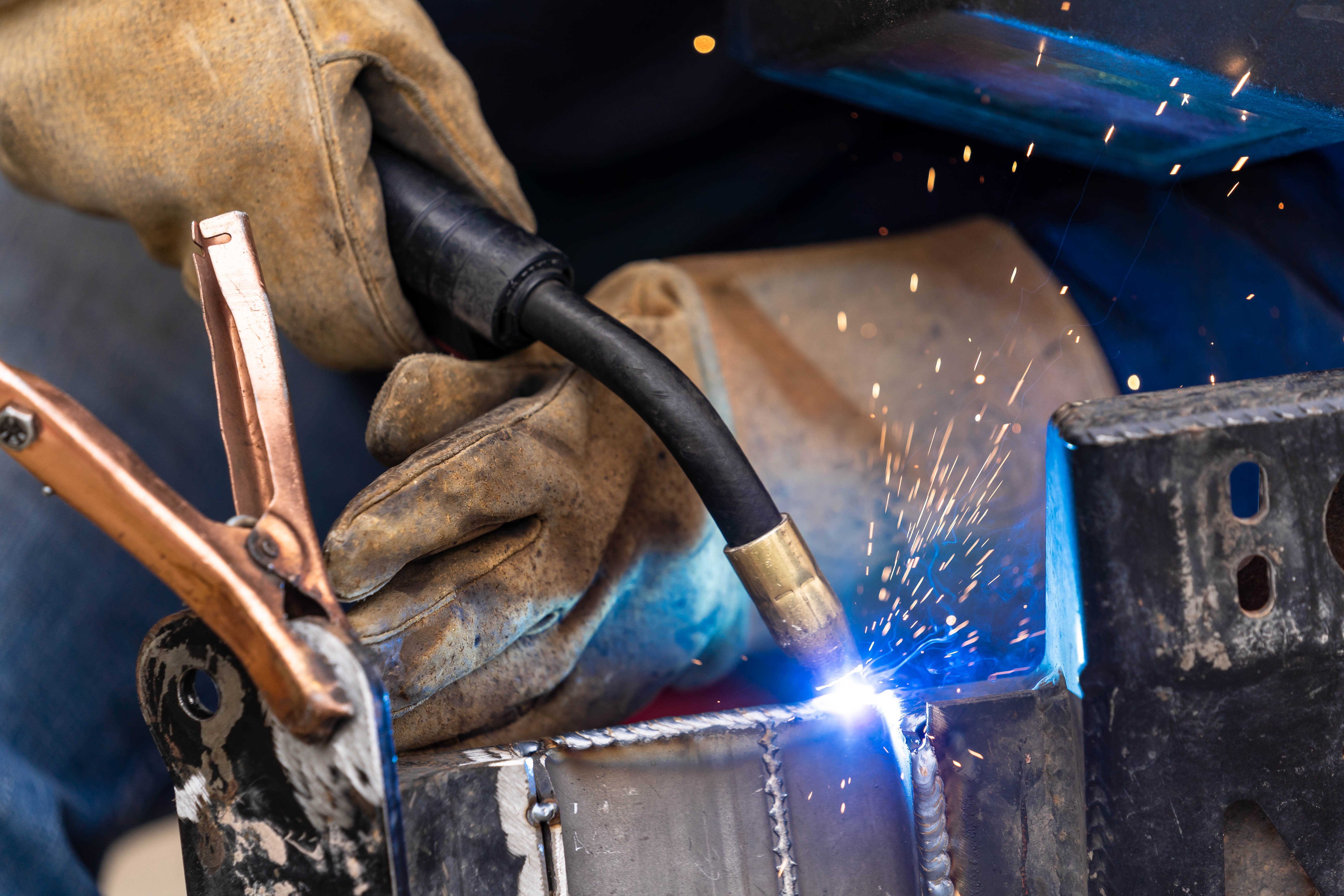
Examiners rely on WPS documentation to confirm that welding procedures are being complied with correctly and that the resulting welds are of high top quality. Designers make use of WPS requirements to design welding procedures that ensure the longevity and reliability of bonded structures.

Vital Tools for Top Quality Welds
Understanding welding WPS criteria is essential for welders to effectively utilize the vital devices needed for producing top quality welds. The type of welding maker needed depends on the welding process being utilized, such as MIG, TIG, or stick welding. Cord brushes and breaking hammers are important for cleaning the weld joint prior to and after welding to eliminate any kind of pollutants that might impact the top quality of the weld.
Trick Methods for Welding Success
To attain welding success, one have to master the crucial strategies important for creating high-quality welds. One important method is keeping the correct arc length. Maintaining the electrode at the optimal range from the work surface is essential for producing strong, consistent welds. Furthermore, managing the travel rate is paramount. Relocating too swiftly can cause insufficient penetration, while moving as well gradually can lead to too much warmth input and possible defects. Correct adjustment of the electrode angle is another vital technique. The angle at which the electrode is held can affect the bead form and penetration of the weld. Moreover, making sure constant gun angle and direction of traveling is vital for harmony in the weld grain. Last but not least, maintaining a stable welding and a constant hand position throughout the process is essential to achieving accuracy and consistency in the welds. By mastering these key methods, welders can raise the top quality of their work and attain welding success.
Ensuring Conformity With WPS Standards
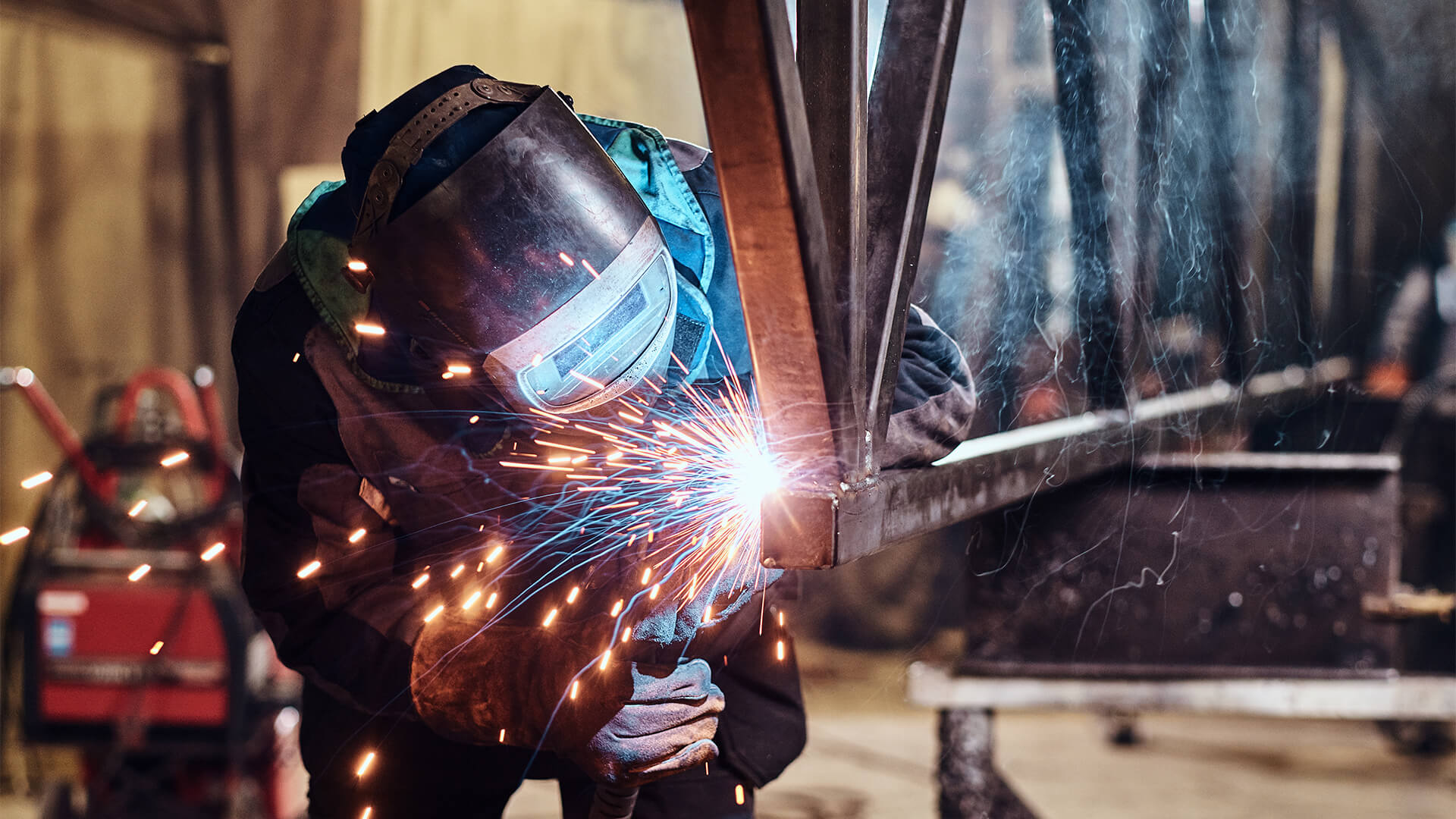
Furthermore, welders ought to undergo training to acquaint themselves with the WPS requirements pertinent to their job. Normal audits and assessments should be performed to confirm that welding activities align with the suggested WPS standards. In addition, keeping in-depth records of welding parameters, equipment calibration, and inspection outcomes is crucial for showing compliance helpful resources with WPS criteria - welding WPS. By carefully sticking to WPS criteria, welders read what he said can ensure that their job fulfills the required top quality degrees and adds to the general success of the welding project.
Troubleshooting Common Welding Issues
To address this, making certain correct cleansing of the base metal before welding and utilizing the proper shielding gas can considerably reduce porosity. Furthermore, distortion, breaking, and spatter are typical welding obstacles that can be mitigated through correct joint preparation, constant heat control, and selecting the proper welding consumables. By completely comprehending these usual welding concerns and their origin creates, welders can successfully repair issues and attain top quality welds.
Verdict
To conclude, understanding welding WPS requirements needs an extensive understanding of the standards, utilizing crucial devices, and executing my sources key techniques for effective welds. Making sure compliance with WPS requirements is critical for generating top quality welds and staying clear of usual welding concerns. By complying with best strategies and methods, welders can attain constant and trusted cause their welding jobs.
In the realm of welding, understanding Welding Treatment Spec (WPS) criteria is an important component that directly affects the top quality and integrity of welds.When diving into the realm of welding practices, a critical element to comprehend is the relevance and ins and outs of Welding Treatment Specification (WPS) requirements. WPS criteria offer a detailed guideline for welding operations, making certain uniformity, quality, and security in the welding process. The kind of welding maker needed depends on the welding procedure being used, such as MIG, TIG, or stick welding.Achieving welding success with the proficiency of vital methods demands a thorough understanding and adherence to Welding Procedure Requirements (WPS) standards.
Report this page